Cement is one of the most essential materials in construction, playing a vital role in binding different components together to form a strong and durable structure. It is a fine powder made from limestone, clay and other minerals, which hardens when mixed with water. Different types of cement are used in construction, depending on the specific needs of a project.
Why Is Cement Important?
Cement is a fundamental material in construction, providing strength, stability and durability to various structures. Its role in infrastructure and building projects makes it indispensable for modern development. Cement is crucial in various construction activities, including the following:
- Building foundations, bridges and highways
- Creating durable concrete structures
- Enhancing the strength and longevity of buildings
Our suggestion: Comprehensive cement purchase guide
Common Properties of Cement
All types of cement share some fundamental properties:
Property | Description |
Binding Ability | Binds aggregates together to form concrete. |
Strength | Provides durability and load-bearing capacity. |
Setting Time | Varies depending on the type of cement. |
Resistance | Some cements are resistant to sulfate, heat, or water. |
Types of Cement and their significance
There are various types of cement, each designed for specific applications. Some are preferred for general construction, while others are used in extreme environmental conditions. Understanding these differences helps in selecting the right cement for durability, cost-effectiveness and safety.
In the next section, we will explore Ordinary Portland Cement (OPC), one of the most widely used types of cement, along with its key properties and applications.
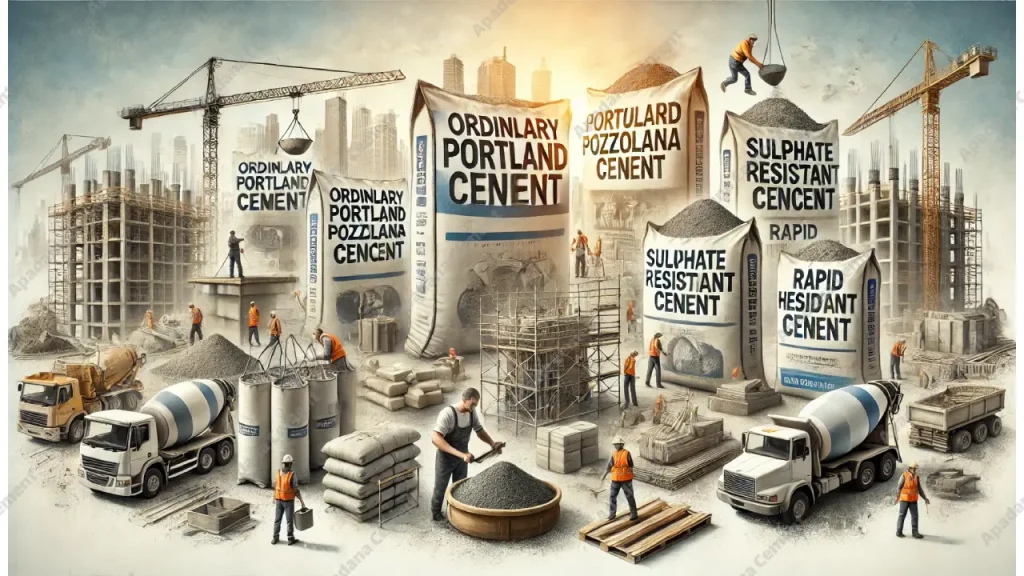
Ordinary Portland Cement (OPC) and Its Applications
Ordinary Portland Cement (OPC) is the most commonly used type of cement in construction. It is made by grinding a mixture of limestone and clay and then heating it in a kiln at high temperatures. OPC is known for its strength, durability and versatility, making it a preferred choice for various building projects.
Grades of OPC and Their Uses
OPC is available in three main grades, classified based on their compressive strength (measured in megapascals, MPa) after 28 days:
Grade | Compressive Strength | Common Applications |
OPC 33 | 33 MPa | Plastering, masonry work, and small-scale structures |
OPC 43 | 43 MPa | Residential buildings, bridges, and precast concrete elements |
OPC 53 | 53 MPa | High-rise buildings, highways, and heavy infrastructure |
Advantages of OPC
- Fast setting time – Ideal for projects requiring quick construction.
- High strength – Provides strong structural integrity.
- Wide availability – It is Easily accessible in most markets.
- Versatile applications – Suitable for concrete, mortar, and plastering.
Limitations of OPC
- Requires proper curing to prevent cracks.
- Less resistant to chemical attacks compared to some other types of cement.
Higher heat generation during hydration, which may cause thermal cracks.
Due to its widespread availability and reliability, OPC remains a dominant choice in construction. However, alternative cements like Portland Pozzolana Cement (PPC) offer additional benefits, which we will discuss in the next section.
Our suggestion: buying cement
Portland Pozzolana Cement (PPC): Properties and Benefits
Portland Pozzolana Cement (PPC) is another commonly used type of cement that is mixed with pozzolanic materials like fly ash, volcanic ash or silica fumes. This combination enhances the properties of cement, providing improved strength, durability and resistance to chemical attacks. PPC is known for being environmentally friendly due to the use of industrial by-products like fly ash, which also reduces carbon emissions during its production.
Advantages of PPC
- Improved Durability: The addition of pozzolanic materials increases the resistance of concrete to sulfate attacks, making it ideal for construction in coastal or industrial environments.
- Reduced Heat of Hydration: PPC generates less heat during the curing process, making it a suitable choice for large mass concrete projects where heat build-up could cause cracking.
- Cost-Effectiveness: Due to the use of supplementary materials, PPC tends to be more affordable than Ordinary Portland Cement (OPC), making it an economical option for large-scale construction projects.
Environmental Benefits: Using industrial by-products helps reduce waste and lower the overall carbon footprint of the cement industry.
Common Applications of PPC
PPC is commonly used in:
- Large-scale infrastructure projects like dams, bridges, and highways
- Buildings in coastal areas where resistance to sulfate attacks is crucial
- Massive concrete works such as foundations, floors, and pavements
While PPC has many advantages, it is essential to choose the right type of cement based on the specific requirements of your construction project. The next section will cover Rapid Hardening Cement, another specialized type of cement designed for projects requiring quick strength development.
Rapid Hardening and Quick Setting Cement
Rapid Hardening Cement and Quick Setting Cement are specialized types of cement designed for projects that require quick construction or early strength development. While they share similarities, they have distinct characteristics and applications.
Rapid Hardening Cement
Rapid Hardening Cement is designed to gain strength faster than regular Ordinary Portland Cement (OPC). This is achieved by modifying the composition of the cement, specifically by increasing the percentage of tricalcium silicate (C3S), which accelerates the hydration process.
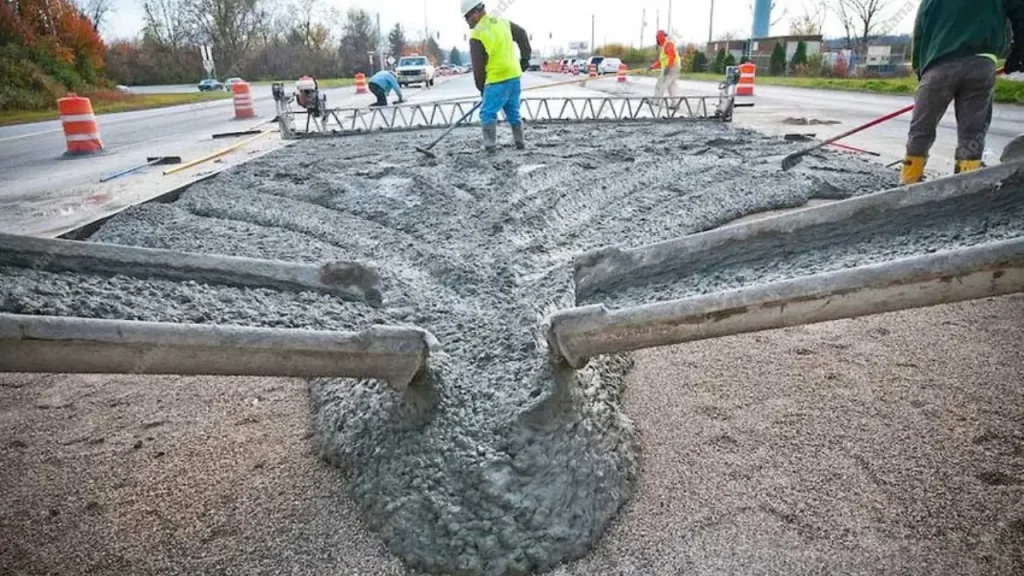
Advantages of Rapid Hardening Cement
- Faster Strength Development: Ideal for projects that require early load-bearing capacity, such as precast concrete and repair work.
- Shorter Construction Time: Reduces the curing time for projects, allowing quicker progress and earlier utilization of concrete structures.
- High Durability: Suitable for cold-weather concreting due to quicker strength gain, preventing freezing of the concrete during curing.
Common Applications
- Precast concrete elements like beams, columns, and slabs
- Cold weather concreting, where rapid strength is crucial
- Road repairs and other quick-turnaround construction projects
Quick Setting Cement
Quick-setting cement, on the other hand, is designed to set quickly rather than harden faster. It has a reduced setting time, meaning it begins to harden rapidly after mixing with water, making it ideal for situations where immediate use is required.
Advantages of Quick Setting Cement
- Immediate Setting: Sets in just a few minutes, preventing seepage in underwater constructions or during rainy weather.
- Minimized Risk of Leaks: This is Perfect for projects that require the prevention of water ingress quickly, such as repairing pipelines or cracks.
- Weather Resistance: Beneficial in conditions where quick setting is necessary due to external environmental factors.
Common Applications
- Underwater construction where quick setting is needed to stop water flow
- Repairing cracks or holes in structures exposed to water
- construction, ensuring no leakage during construction
Both Rapid Hardening Cement and Quick Setting Cement are valuable for specific applications, but choosing between them depends on whether you need faster strength development or quicker setting times. The next section will dive into Specialty Cements, which include Sulphate-Resistant, Low Heat, and White Cement, designed for more specific needs in construction.
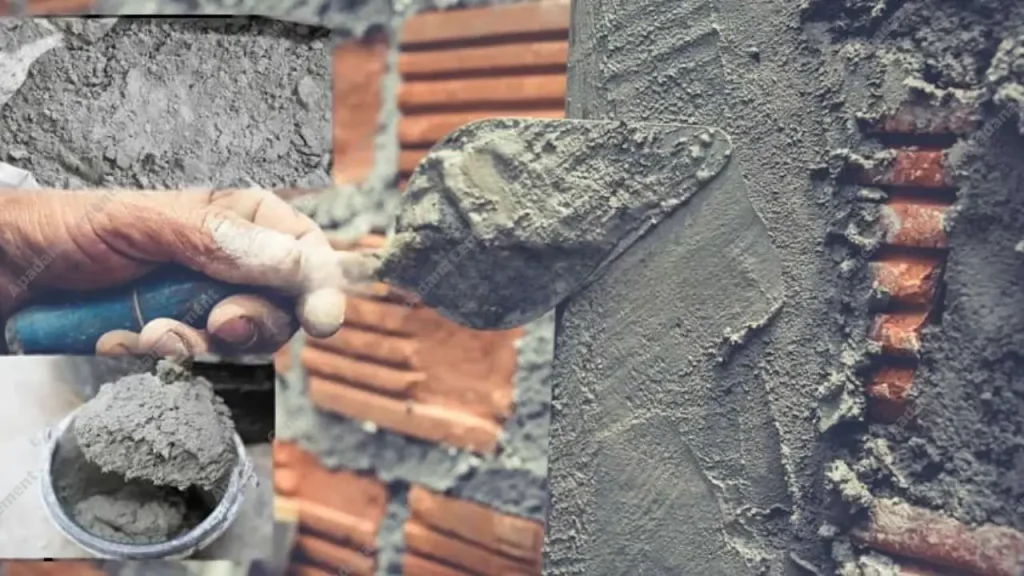
Specialty Cements: Sulphate-Resistant, Low Heat and Others
Specialty types of cement are designed to meet specific needs in challenging conditions. They offer enhanced properties such as better chemical resistance, reduced heat generation, and superior aesthetics. Key examples include Sulphate-Resistant Cement (SRC), Heat Cement, and White Cement.
Sulphate-Resistant Cement (SRC)
SRC is ideal for areas with high sulphate concentrations, such as coastal regions, where it helps prevent cracking and deterioration caused by sulphate attacks. It is highly durable and resistant to harsh chemicals, making it suitable for water treatment plants and sewage systems.
Low Heat Cement
This type of cement is used for large-scale projects like dams to minimize heat buildup during hydration, preventing thermal cracking. It enhances durability by reducing heat generation, making it perfect for cold-weather construction and massive concrete works.
White Cement
Produced with raw materials free from iron oxide, White Cement is used in decorative applications due to its aesthetic appeal and smooth finish. It is often used for architectural elements, flooring, tiles, and mosaics. Choosing the right type of cement ensures superior performance and longevity in demanding environments.
Comparison of Different Types of Cement
Cement Type | Strength | Durability | Cost | Best for |
Ordinary Portland Cement (OPC) | High initial strength | General durability | Moderate | General-purpose projects |
Portland Pozzolana Cement (PPC) | Slower strength gain | Better chemical resistance | More cost-effective | Infrastructure, coastal areas |
Rapid Hardening Cement | Faster strength development | High strength in less time | More expensive | Fast construction, early strength needs |
Quick Setting Cement | Same as OPC, quick setting | Less strength in the short term | Slightly cheaper | Underwater or rainy-weather applications |
Sulphate-Resistant Cement (SRC) | Moderate strength | Best for aggressive environments | Higher cost | Water treatment plants, sewage systems |
Low Heat Cement | Moderate | Ideal for massive works | Similar to OPC | Large concrete works, dams |
White Cement | Moderate | Aesthetic appeal | Expensive | Decorative works, facades, tiles |
Conclusion
In conclusion, understanding the different types of cement available is crucial for the success of any construction project. The choice of cement directly affects the durability, strength, and overall performance of the structure. From the general-purpose Ordinary Portland Cement (OPC) to specialized cements like Portland Pozzolana Cement (PPC), Rapid Hardening Cement, and Sulphate-Resistant Cement, each type has its unique advantages tailored to specific needs.
Choosing the right type of cement ensures:
- Structural integrity by meeting the project’s strength and durability requirements.
- Cost-efficiency by selecting the most suitable cement type for the conditions, avoiding overuse of more expensive, specialized cements where not needed.
- Long-term performance, with the right cement offering resistance to external factors like moisture, chemicals, or heat, depending on the environment.
It’s essential to consult with construction professionals and understand the specific requirements of each project before selecting a type of cement. By doing so, you’ll ensure the project is completed efficiently, safely, and within budget.
By following these guidelines and making informed decisions, construction professionals can optimize both the materials and methods for each job. Always consider factors such as types of cement, setting time, strength development, and environmental conditions when making your choice. Remember, the right cement can make a significant difference in the long-term success of your construction project.
What are the different types of cement used in construction?
There are several types of cement, including Ordinary Portland Cement (OPC) for general use, Portland Pozzolana Cement (PPC) for better durability, Rapid Hardening Cement for quick-setting projects, Sulphate Resistant Cement for structures exposed to sulphates, and White Cement for decorative purposes.
Which type of cement is best for house construction?
Ordinary Portland Cement (OPC) 43 or 53 grade is commonly used for house construction due to its strength and versatility. However, Portland Pozzolana Cement (PPC) is also a great choice as it offers better resistance to moisture and chemical attacks, making buildings more durable.
What is the difference between OPC and PPC cement?
OPC (Ordinary Portland Cement) sets faster and has higher early strength, making it ideal for projects requiring quick construction. PPC (Portland Pozzolana Cement) takes longer to set but provides better long-term durability and resistance to chemicals, making it more suitable for humid or coastal areas.