Portland Pozzolana Cement (PPC) is a type of blended cement that has become increasingly popular in modern construction due to its durability, workability, and eco-friendly nature. It is produced by mixing Portland cement clinker with pozzolanic materials such as fly ash, silica fume, or volcanic ash. One of the key reasons for its widespread adoption is the wide range of applications it supports—the uses of PPC cement extend across residential buildings, infrastructure projects, and marine structures. In addition to its versatility, PPC cement offers several technical advantages, including improved long-term strength, higher resistance to chemical attacks, and reduced heat of hydration, making it both a cost-effective and sustainable option in today’s construction industry.
In this article, we will explore the manufacturing process of PPC cement in detail, how to check its quality and its various applications in construction. Additionally, we will discuss the advantages of using PPC cement and why it is a preferred choice in many construction projects worldwide.
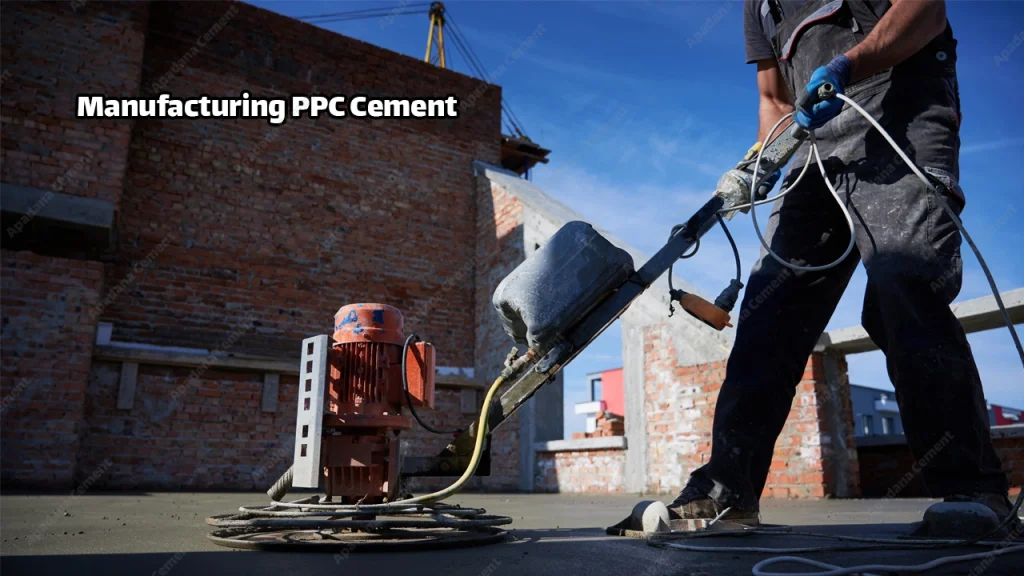
Our suggestion: buying cement
How is Portland Pozzolana Cement Made?
PPC cement is produced through a systematic process that enhances its properties while ensuring sustainability. The manufacturing process includes several crucial steps that ensure the final product meets the required strength and quality standards. Below are the key steps involved in its manufacturing:
1. Raw Material Selection
- The primary raw materials used are Portland cement clinker, gypsum and pozzolanic materials like fly ash, volcanic ash or silica fumes.
- Pozzolanic materials play a crucial role in enhancing the properties of PPC cement by reacting with calcium hydroxide to form additional cementitious compounds.
- These materials are selected based on their chemical composition to ensure optimal performance of the final product. The selection process is rigorous to maintain consistency and quality across different batches of cement.
2. Clinker Grinding
- The Portland cement clinker which is produced by heating limestone and clay in a kiln at high temperatures (around 1400-1450°C), is ground into a fine powder.
- Gypsum is added during grinding to regulate the setting time of the cement and prevent flash setting.
- The grinding process ensures that the cement particles are of the required fineness, which affects the strength and workability of the final product.
3. Mixing with Pozzolanic Materials
- The finely ground clinker is blended with pozzolanic materials in a specific ratio, typically ranging between 15-35% depending on the intended use.
- This mixture is then processed to ensure uniformity and consistency. The pozzolanic materials react with the calcium hydroxide released during hydration to form additional cementitious compounds, enhancing the strength and durability of the cement.
4. Final Grinding and Packaging
- The blended cement undergoes further grinding to achieve the desired fineness, ensuring optimal performance in various construction applications.
- Once the cement reaches the required quality standards, it is packed in bags and transported for distribution.
- Quality control measures are implemented at this stage to ensure that the cement meets national and international standards for strength, setting time, and durability.
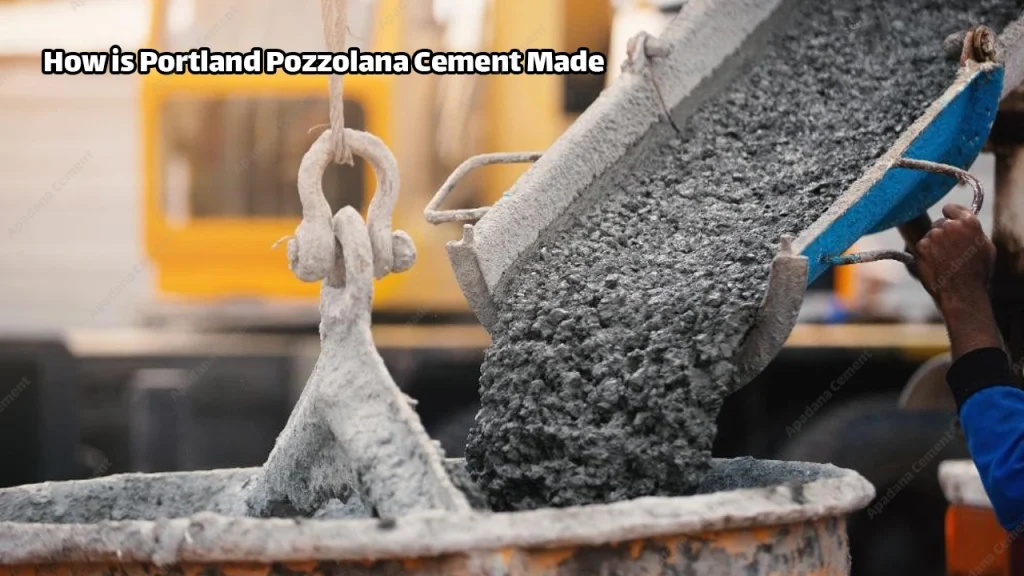
More articles: Understanding Different Types of Cement and Their Uses
How to Check PPC Cement Quality?
To ensure that PPC cement meets construction standards, certain quality checks should be performed before use. These checks help in verifying the consistency and reliability of the cement, preventing issues in construction projects.
1. Physical Inspection
- The cement should have a uniform color, free from lumps and a smooth texture.
- Lumps indicate moisture absorption which can affect the performance of the cement.
- The presence of lumps suggests improper storage conditions and should be avoided.
2. Setting Time
- The initial setting time should be at least 30 minutes to allow for proper handling and placement.
- The final setting time should not exceed 600 minutes to ensure that the cement hardens within a reasonable period.
- The setting time can be tested using a Vicat apparatus, which measures the time taken for a standard needle to penetrate a cement paste of standard consistency.
3. Compressive Strength
- PPC cement should have a minimum compressive strength of 33 MPa after 28 days.
- Compressive strength testing is done using a compression testing machine on standard mortar cubes prepared with cement and sand.
- Higher strength values indicate better performance and durability of the cement in construction applications.
4. Fineness Test
- The fineness of PPC cement should be around 300-400 m²/kg.
- A finer cement ensures better reactivity and enhances the strength development of concrete.
- The fineness can be tested using a Blaine air permeability apparatus.
5. Soundness Test
- This test ensures that the cement does not expand excessively after setting, preventing cracks in structures.
- Soundness testing is conducted using the Le Chatelier apparatus, which measures expansion due to the presence of uncombined lime and magnesia.
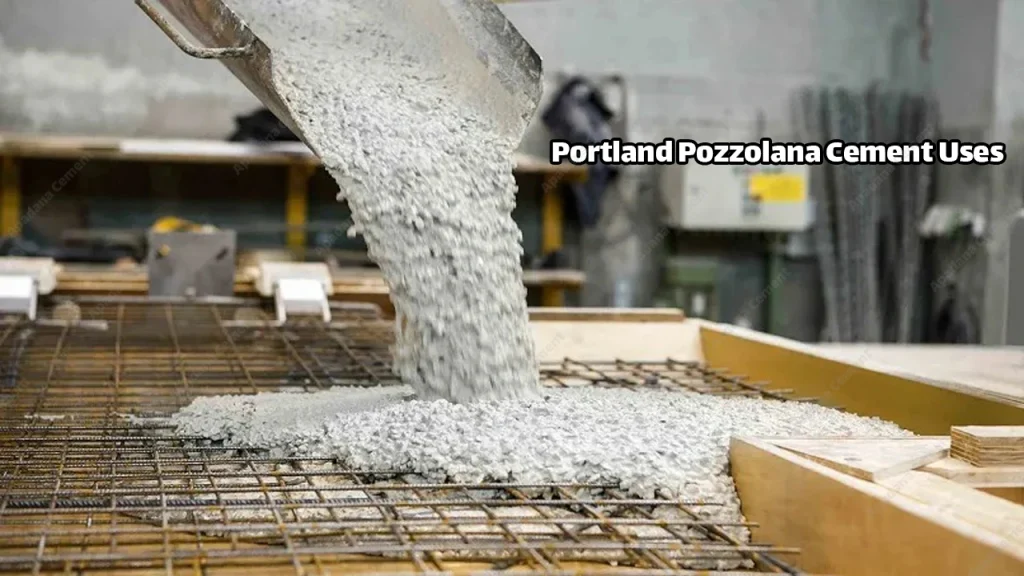
More articles: Comprehensive cement purchase guide [2025 Update]
Uses of PPC Cement
PPC cement is widely used in different construction applications due to its superior durability and resistance to environmental factors. Its unique properties make it a preferred choice for various structural and non-structural applications. Some common uses include:
1. Residential and Commercial Buildings
- PPC cement is commonly used in the construction of houses, apartments, and office buildings due to its long-lasting strength and durability.
- It ensures better resistance to weather conditions, reducing maintenance costs over time.
2. Bridges and Dams
- Due to its resistance to chemical attacks and lower heat of hydration, PPC cement is ideal for massive structures like bridges and dams.
- The reduced heat of hydration prevents the formation of thermal cracks, ensuring long-term stability.
3. Road Construction
- PPC cement is often used in concrete roads and pavements due to its ability to withstand heavy traffic loads and weather variations.
- It provides better durability, reducing repair and maintenance costs over time.
4. Marine and Hydraulic Structures
- Its resistance to sulfate and chloride attacks makes it suitable for marine structures, sewage treatment plants, and water tanks.
- PPC cement prevents corrosion of reinforcement, enhancing the lifespan of structures exposed to aggressive environments.
5. Plastering and Masonry Work
- PPC cement provides excellent adhesion and smooth finishes, making it ideal for plastering and masonry applications.
- The fine particles enhance workability, reducing water demand during mixing.
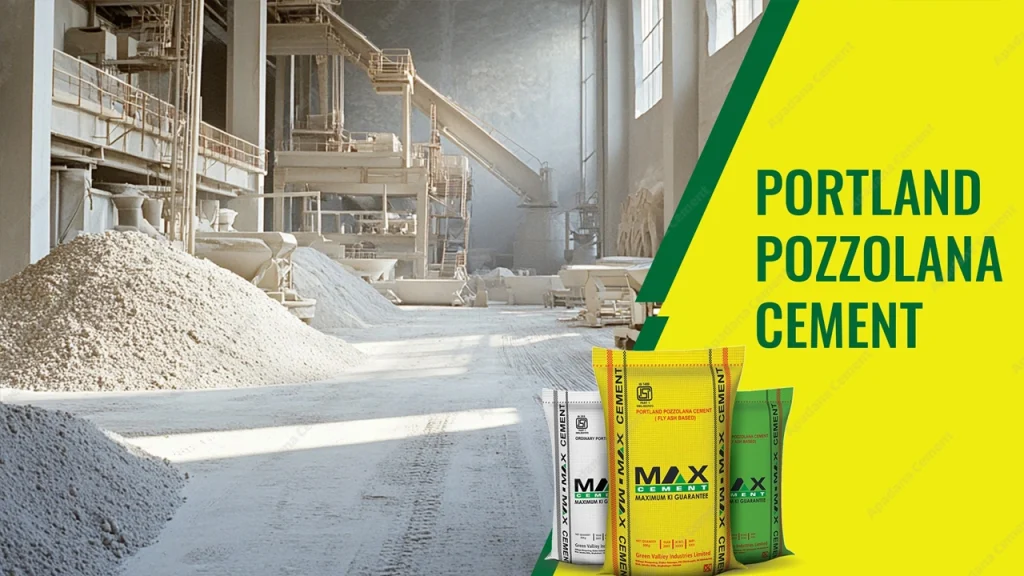
پیشنهاد ما: خرید سیمان
Advantages of Portland Pozzolana Cement
PPC cement offers several benefits that make it a preferred choice in construction:
- Enhanced Durability: It improves the long-term strength of structures, making them more resilient.
- Eco-Friendly: The use of fly ash or other pozzolanic materials reduces carbon emissions and energy consumption.
- Lower Heat of Hydration: This minimizes the risk of thermal cracks in large concrete structures.
- Better Workability: The fine particles of PPC cement enhance workability, reducing water consumption during mixing.
- Increased Resistance to Chemical Attacks: It provides better protection against sulfates, alkalis, and chlorides, ensuring longer-lasting structures.
Difference Between PPC and OPC Cement
Portland Pozzolana Cement (PPC) and Ordinary Portland Cement (OPC) are two of the most commonly used cement types, but they differ significantly in composition, performance, and applications. OPC is made primarily from clinker and gypsum, while PPC contains pozzolanic materials such as fly ash, silica fume, or volcanic ash in addition to clinker and gypsum. These pozzolanic materials react with calcium hydroxide released during hydration, forming additional cementitious compounds that enhance durability and strength over time.
One of the main differences between PPC and OPC is their strength development. OPC gains strength faster in the initial stages, making it suitable for projects requiring quick setting and early strength, such as road construction and precast structures. On the other hand, PPC has a slower strength gain but ultimately achieves higher durability and resistance to chemical attacks, making it ideal for marine structures, bridges, and buildings exposed to harsh environments. Additionally, PPC has a lower heat of hydration, reducing the risk of thermal cracking in mass concrete applications. Its eco-friendly nature, due to the use of industrial by-products like fly ash, makes it a preferred choice for sustainable construction.
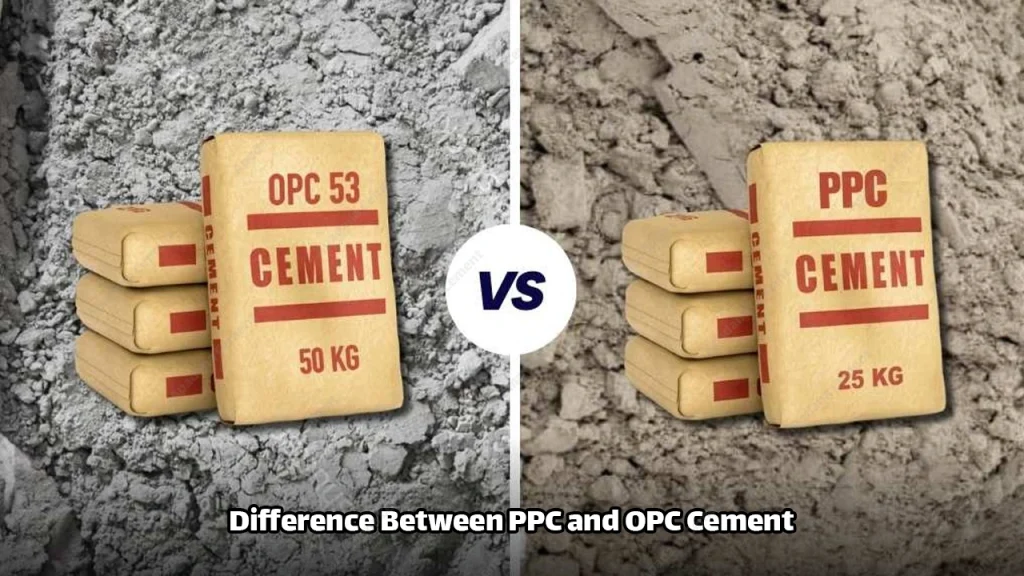
Conclusion
Portland Pozzolana Cement is a sustainable and high-performance alternative to ordinary Portland cement. Its manufacturing process involves blending clinker with pozzolanic materials, which enhances durability and workability. PPC cement is widely used in residential, commercial, and infrastructure projects due to its superior strength, resistance to chemical attacks, and eco-friendly properties. By understanding its advantages and quality checks, builders and engineers can make informed choices for durable and efficient construction projects.
To buy cement, you can use Apadana Company. This company provides you with the best cements available on the market. For advice and purchase of various types of cement, you can use the communication methods available on the contact us page.
What are the primary applications of Portland Pozzolana Cement (PPC)?
Portland Pozzolana Cement (PPC) is widely used in various construction projects due to its enhanced durability and resistance to chemical attacks. Common applications include hydraulic structures like dams and bridges, marine structures, sewage treatment plants, and residential buildings. Its reduced heat of hydration makes it particularly suitable for mass concrete works, minimizing the risk of thermal cracking.
How does PPC cement contribute to environmental sustainability in construction?
PPC cement incorporates pozzolanic materials such as fly ash, which are industrial by-products. By utilizing these materials, PPC reduces the need for clinker, thereby lowering carbon dioxide emissions associated with cement production.
Can PPC cement be used for plastering and masonry work?
Yes, PPC cement is suitable for plastering and masonry applications. Its fine particles enhance workability and provide a smooth finish, making it ideal for such purposes. Additionally, the improved adhesion properties of PPC contribute to the longevity and durability of plastered surfaces and masonry structures.